Projects
Nunavut Housing Mould Mitigation Program – NU
Dillon was retained in December, 2017 by Nunavut Housing Corporation (NHC) to complete this Residential Units Mould Mitigation Program. This project is a culmination of approximately three years of work conducted by Dillon, in collaboration with NHC, Local Housing Organizations (LHOs), our sub-consultant RDH Building Science (RDH), and various Nunavut-based contractors in designing, building, and testing various design strategies aimed at mitigating potential mould impacts in NHC’s existing stock.
Various other projects were completed by Dillon in conjunction with this project to assist in understanding the magnitude and extent of mould impacts in NHC housing stock. These supporting projects have included the detailed assessment of over 500 housing units across Nunavut over the last three years.
As introduction to this project, it is important to first understand the context for why this project was required. Studies completed by Dillon on behalf of NHC have indicated that approximately 80% of NHC’s existing housing stock have mould impacts, with approximately 20% of the units having greater than three square metres of mould on interior visible surfaces. Mould remediation work conducted by NHC since 2017 in various communities throughout Nunavut has indicated that it is not uncommon for the mould impacts to extend into the interior of the floor, wall and/ or roof assemblies. In numerous cases the high moisture conditions within the building assembly structure has also resulted in wood rot ranging from minor to severe, including cases impacting the structural integrity of some wood members.
One of the common design features of residential units in Nunavut is the use of an unvented cathedral ceiling design, also called a “hot roof” design. It is unknown why this roof design was adopted decades ago; however, it is suspected that snow penetration into traditional vented roof assemblies prompted adopting the unvented roof assembly design. While this design has been successfully employed in other locations, it has been found to be problematic in many cases in Nunavut due to condensation formation within the unvented roof assembly leading to mould generation and in some cases severe rot.
Although unconfirmed, it is suspected that high humidity conditions associated with overcrowding, combined with potential vapour barrier issues and extreme cold have led to the observed prevalence of condensation formation within the unvented roof assembly. As described in this summary, a key focus of this project included exploring methods to introduce ventilation into the cathedral roof assembly, while mitigating potential snow penetration through the roof vents.
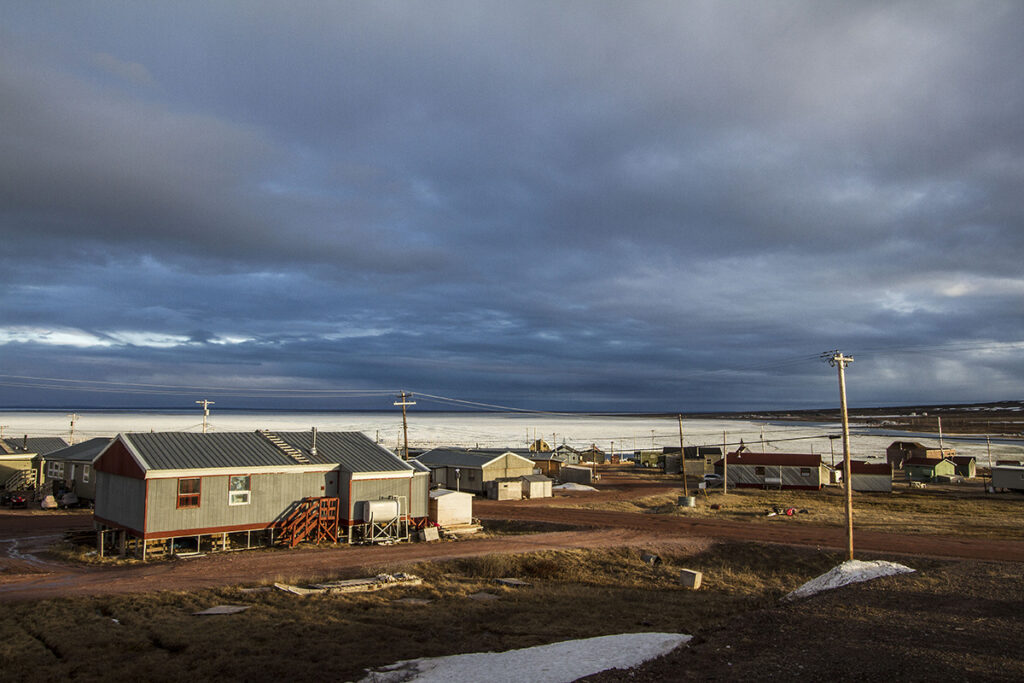
The root-causes of mould impacts observed in the housing units were studied in detail as part of this project. In summary, there are multiple root causes of the mould observed in the housing units, including:
- Design, maintenance, and construction issues related to the building envelop;
- Design, operation, and maintenance of building ventilation systems; and
- Tenant damage and negative behavior issues (e.g., disconnecting ventilation equipment).
It is not uncommon for multiple potential root causes of mould to be present in impacted units. In addition to these potential root causes, the impact of the current housing crisis on the prevalence of mould impacts observed in Nunavut should not be underestimated. The housing crisis is resulting in higher levels of occupancy in some homes, and thus elevated levels of humidity in the homes associated with human respiration. This is particular evident where existing building ventilation systems are not present or not operating effectively per the root causes noted above. In summary, the high levels of occupancy in the homes potentially exacerbates and increases the frequency of mould generation in the homes in combination with the other root causes noted above.
Dillon was commissioned by NHC to understand the root causes of mould generation in their existing housing stock, study and identify potential strategies for preventing mould generation, followed by detailed design of pilot test homes to investigate the performance of these design and operational changes.
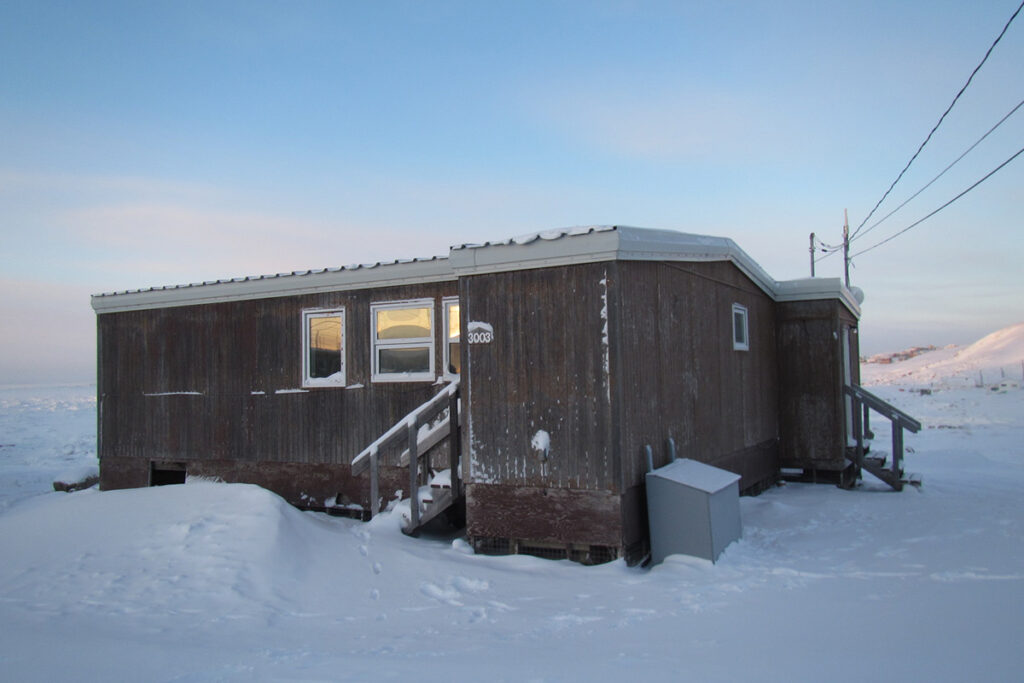
The overall objective for this program was to develop new design recommendations for the building envelop and mechanical ventilations, as well as architectural features, to assist in mitigating future mould generation.
This project was executed in the following five phases:
- Phase 1: Mould Root Cause Analysis
- Phase 2: Problem Formulation, Gap Analysis, and Air Monitoring Program
- Phase 3: Mould Mitigation Options Analysis
- Phase 4: Mould Mitigation Pilot Testing Program
- Phase 5: Mould Mitigation Design Recommendations
In developing the strategy for this project, the approach was to adopt a holistic approach to addressing many of the potential root causes of mould in relation to building envelop and mechanical ventilation system design. In addition, the project included testing of various strategies aimed at mitigating the impact on the building envelop due to potential negative tenant behavior, such as negative impact to the building vapour barrier due to interior wall damage.
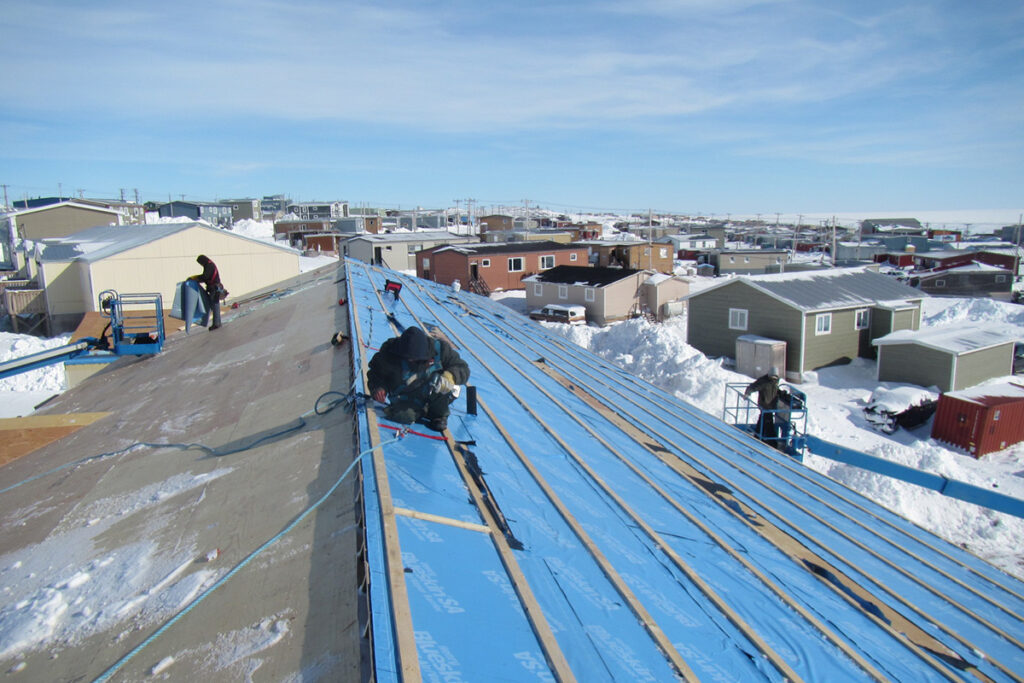
It is intended that the design recommendations from this project would inform the design of new builds regarding potential design strategies to assist in mitigating mould generation in newly constructed units. In addition, the design recommendations are intended to assist in the detailed design of retrofit requirements in current housing units impacted by mould and requiring remedial measures.
Challenges and Innovative Engineering Solutions
As noted in the previous section, the project was initiated with Phase 1, an assessment of the root causes of mould generation. The results of this assessment in relation to building envelop and mechanical system related root causes are summarized as follows:
Building Envelop Related Potential Root Causes:
- Cold being transmitted through wood members resulting in condensation/mould formation (i.e., “thermal bridging”);
- Lack of ventilation/air circulation in interior roof cavities utilizing an unvented, cathedral roof design (i.e., “hot roof” design);
- Missing or damaged insulation in walls, ceilings, floors and/or around windows; and,
- Poor vapour barrier seal due to poor construction, wall damage, and/or maintenance work.
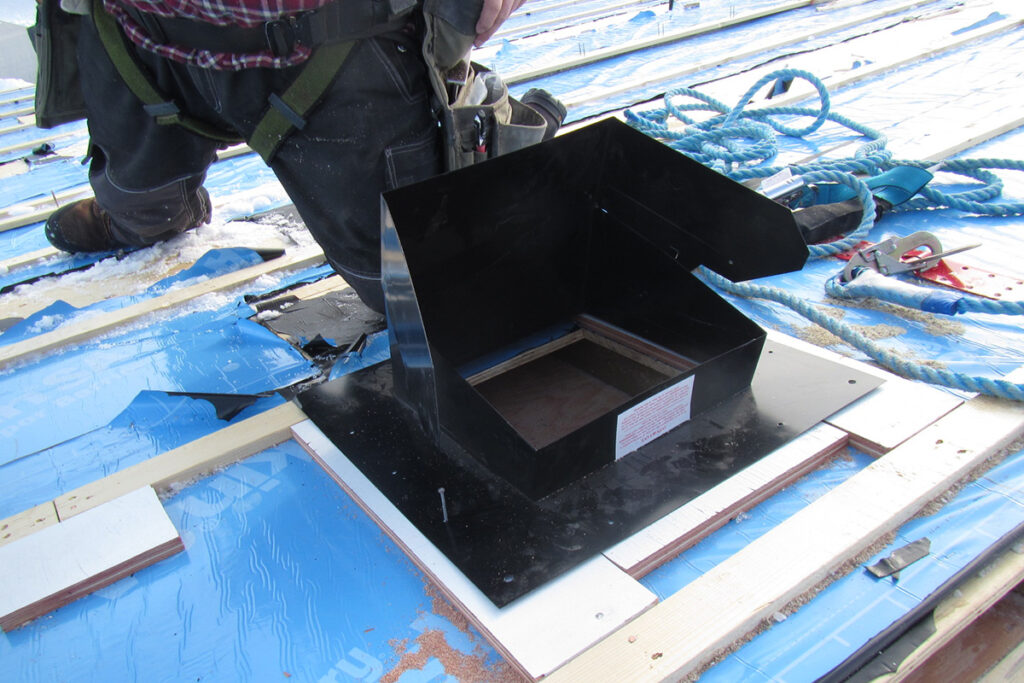
Mechanical Related Potential Root Causes:
- Inadequate ventilation systems in some units and/or lack of ventilation of high humidity areas such as building crawlspaces;
- Some Heat Recovery Ventilators (HRVs) undersized due to high occupancy/over-crowding;
- Lack of regular maintenance and cleaning of HRV filters resulting in poor air exchange;
- HRV core freezing resulting in periods of continuous operation in recirculation mode, thus not providing ventilation during these periods;
- Leaking plumbing fixtures; and,
- Leaking water and sewage tanks.
Phase 2 of the project included indoor air monitoring testing on a number of occupied residential units throughout Nunavut.
The testing included monitoring of CO2, temperature, and relative humidity (RH) levels in the homes throughout the day over an approximate two week period. The results of this testing indicated the following:
- A direct correlation between RH and CO2 levels was observed suggesting that the primary driver for elevated relative humidity was due to human occupancy, particularly in overcrowded units.
- The CO2 levels measured in the housing units assessed were typically elevated above comfort levels which is considered above 1,000 ppm. Above this CO2 level, occupants tend to become unsatisfied with indoor air quality and symptoms such as drowsiness can be experienced. These elevated CO2 levels indicated potential inadequate air circulation relative to the occupancy and activities in the units.
- Relative humidity ranged from excessively low to high.
The options analysis was completed during Phase 3 of the project and included research into best practices for residential unit building envelop and mechanical ventilation system design for arctic conditions. In summary, although some research was available in Canada and internationally, limited data was publically available regarding the actual performance of various design concepts for residential building envelop and mechanical ventilation systems. Furthermore, the unique arctic conditions in Nunavut, combined with high occupancy levels associated with the current housing shortage, required design and field testing of full scale pilot testing units to confirm the performance characteristics.
Phase 4 of the project encompassed design, construction, and monitoring of the pilot test units. The units selected for testing were located in Arviat, Igloolik, and Baker Lake and included a total of five existing buildings comprised of single family dwellings and multiplex units, ranging in age from over 40 years old to less than 10 years old. All units selected for testing had existing mould impacts, and in some cases wood rot due to frequent wetting arising from condensation in internal wall and/or roof cavities. Remediation of existing mould impacts and/or structural repairs to the buildings were incorporated into the pilot test unit retrofitting program.
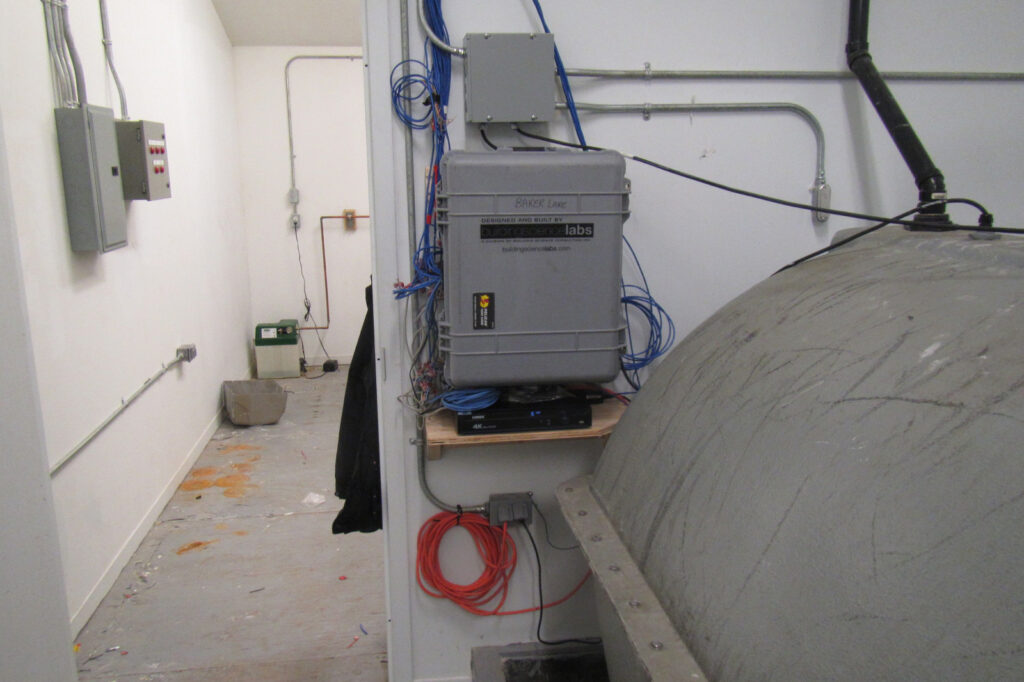
Summary of Pilot Testing Program
In summary, the pilot testing program was successful. Insulation strategies for exterior wall and roof assemblies demonstrated effective condensation and thermal bridging control over the winter months. The roof assembly venting strategies also proved effective in controlling moisture content and humidity levels in the roofs. The testing further demonstrated that the unique soffit vent designs were effective in mitigating potential snow intrusion through the vents.
In addition to the building envelop testing, the mechanical ventilation test results were also positive. Relative humidity levels were maintained below 30% over the winter months, and CO2 levels were maintained around 1,000 ppm.
The pilot testing results were used to develop a “tool box” of design strategies for the building envelop and mechanical ventilation systems for future review and application during mould remediation and retrofit work, as well as assist in informing future new build designs. In addition, the pilot test units remain fully occupied and the monitoring systems remain in place and operational to facilitate long-term monitoring of the building envelop and mechanical systems performance.
Awards
- Award of Merit, Nunavut Housing Corporation, Northwest Territories and Nunavut Association of Professional Engineers and Geoscientists, 2021
Project Details
Project Partner: Nunavut Housing Corporation
Business Unit: Facilities
Service Offering: Facility Assessments